YEデジタルは、変化の激しい物流業界を「倉庫自動化に特化したWES」でリードします。
【第4回】ハード効率運用のカギはソフト!
【執筆】菊田一郎 エルテックラボ 代表/物流ジャーナリスト
本シリーズ第1回で示した「物流センター自動化のロードマップ」のレベル2~4で、筆者は導入対象になる主なハード=マテハン機器・物流ロボット等として以下を挙げました。
<従来型マテハン機器>
・各種ラックと立体自動倉庫 ・自動仕分けなどコンベヤ ・AGV(無人搬送車) ・デジタルピッキングステム(DPS)
・デジタルアソートシステム(DAS) ・パレタイザ ・自動包装機、梱包機 ・ハンディターミナル、バーコードリーダ
・RFIDなどIoTシステム
<物流ロボット>
・AMR(自律型搬送ロボット) ・GTP棚搬送ロボット ・自動ピッキングロボット(ケース、ピース) ・各種のロボット自動倉庫
「レベル3」以上になると、これらのハードウェアをいくつも導入し、WMSに連携させて使う現場になります。「レベル4」になると、先に示したようなベストプラクティスの事例では、主要設備だけでも十数種を数えたりします。こうして導入ハードがロボットのように知能を備えて高度化・複雑化するほど、また連動させるハードが増えるほど、それらをつなぎ、コントロールする「ソフトウェア」が、「ものすごく重要になる」、という話を今回と次回で書こうと思います。
物流ロボットの生産性を左右するソフトウェア
![モノタロウ猪名川DCに導入されたラックル[MonotaRO提供]](/jp/img/product/smartfactory/mmlogi/column/s01-04/image1.jpg)
写真1 モノタロウ猪名川DCに導入されたラックル[MonotaRO提供]
GTPロボットから行きましょう。前回紹介したモノタロウの事例で、同社の笠間ディストリビューションセンターに導入された日立製作所の「Racrew(ラックル)」は300台以上。その後の2022年に稼働した猪名川ディストリビューションセンターには800台以上が導入され、搬送する保管棚の方はその何倍も必要ですから、その数は笠間で約6,000本、猪名川で約10,000本にもなります。その棚を保管エリアと多数の入出庫ステーションとの間で、1日に数十~数百回も搬送する……すごいボリュームです。
GTPピッキングシステムの運用効率を高める最重要ポイントは、ステーションの「作業者に手待ちをさせぬよう、切れ目なく商品/棚を供給する」こと。だったら棚とロボットの数を増やせばいい…なんてわけでなく、冗長すぎるムダ投資にならぬよう、「最小限の棚とロボット台数で最大のパフォーマンスを出せる仕組みを設計し、運用」しないといけません。
ここでカギを握るのは、疑いなくソフトウェアです。ポイントになるのは……
②ロボットはどんな経路で、互いにぶつからぬよう走行してステーションまで届け、帰りはどのコースを通り、今度はどの位置に棚を戻すのか。
…写真1はラックルを導入したモノタロウ猪名川DCの、前回とは別角度の写真です。この数のAGVと棚の搬送に関する運用とコントロールは、ものすごく複雑になります。その時、最適運用に必要なソフトウェア/アルゴリズムの中身は、以下のようになるでしょう。
②ロボット/ルート生成・走行制御システムで、受注状況に応じて最短・最速・安全走行できるようコントロール。GTPロボットではAIによる学習機能を持つ機種が多く、①と合わせて常により効率的な棚ロケーション調整と、ロボットの走行ルート調整を行い自ら進化。
……ロボットは「どう動くか」というハード機能ももちろん大切ですが、これは技術向上でいずれ成熟化し差別化しにくくなっていく。物流ロボットはすでに、この段階に入りつつあります。とすれば勝負は、「どう動かすか」。ソフトウェアで差がつきます。それを左右するのが上のようなソフトの作りこみです。それからもう1つ、「中心者の情熱と執念」を忘れてはいけません。 「え、情熱と執念? ロボットとソフトの話じゃないの?なんでいきなりアナログ話?」 …と思われましょうが、情熱も執念も目に見えないので広義のソフトと考えられなくもない。実例を挙げましょう。
物流ロボットの生産性を左右する執念と情熱
![写真2 オルビス東日本流通センターのAGVシステム[筆者撮影]](/jp/img/product/smartfactory/mmlogi/column/s01-04/image2.jpg)
写真2 オルビス東日本流通センターのAGVシステム[筆者撮影]
今度は小型AGVの事例ですが、イメージ的には物流ロボットに見えますね(写真2)。化粧品・健康食品のEC・店舗販売で知られるオルビスの東日本流通センターにおいて、通販専用出荷ラインに導入されたAGVシステムです。両手で持ちあがるサイズの小型AGV(中国リビアオ社のt-Sort+を改造)を、なんと一挙に330台も導入。ダブルループラインを雲霞の如く、大河のように流れていく様は、じつに壮観です。
AGV1台に顧客の1オーダーを割り当て。周囲22か所のピッキングステーションのうち受注商品のある場所だけにAGVは立ち寄り、作業者が商品をデジタルピッキング、バーコード検品の上でAGVに載ったプラコンに投入。全部完了したプラコンは写真の手前側の34か所の梱包ステーションへと運ばれ、商品は出荷ラインへ。GTPでもAMRでもない、世界にも例のない運用です。
筆者はこの現場を2度取材し、熟考しました。確かにAGVは床面下のRFIDで位置を確認しながらスイスイと滑らかに動き、ステーションには前後2方向からアクセスして作業者の手待ちを最小化するハード機能を発揮します。でも明らかに、本システムのキモはソフトです。この仕組みで運用最適化のポイントは皆さん、どこにあると思われますか?(制限時間10秒)
…………はい、時間です!…………
答えは…「商品ロケーション配置の最適化」です。本システムで回避すべきボトルネックは、ステーションでのAGVの渋滞発生(偏れば他では手空きも出る)です。これを避けるには?
②販売政策と連動し、キャンペーン商品は優先ロケに移動
③過去データ分析で季節・月間・週間波動や予測を反映、配置を細かくメンテナンス
…前項①とも重なりますが、このような対応が執念で続けられているのです。それを徹底できているのは、オルビスの物流パートナーとして30年以上の現場運用で経験を蓄積した流通サービスの担当者が、オルビスの物流特性を知り抜いているから。同センターでは、ライバル各社の見学希望も平気で受け入れています。「本当のノウハウは、眼に見えないところにあるから」と、この斬新なシステムの開発・導入を推進したオルビスの物流責任者さんは、涼しい顔で言うのです。
その時、私はこのシステムの本質を理解しました。物流パートナーが30余年にわたって執念で積み重ねてきた経験・ノウハウと、荷主側責任者の物流高度化への情熱とがあいまって、初めて、この自動化設備の最適運用が実現されているのだと。一滴の血も流れていない機械設備なんですが、ソフトウェアと現場運用には、熱い魂が込められているのです。
本システムは作業員を約3割削減、1件あたり出荷コストを約2割削減するという成果を生み出しました。間もなく稼働3年になる今も、極めて順調に走り続けています。
次回は【物流センター自動化のステップ編(全5回)】の最終回。「ハード運用最適化の勝負を決めるソフトウェア」の本丸、WMS(倉庫管理システム)とWES(倉庫実行システム)の役割について述べようと思います。
(つづく)
YEデジタルは、変化の激しい物流業界を「自動倉庫に特化したWES」でリードします。
筆者プロフィール
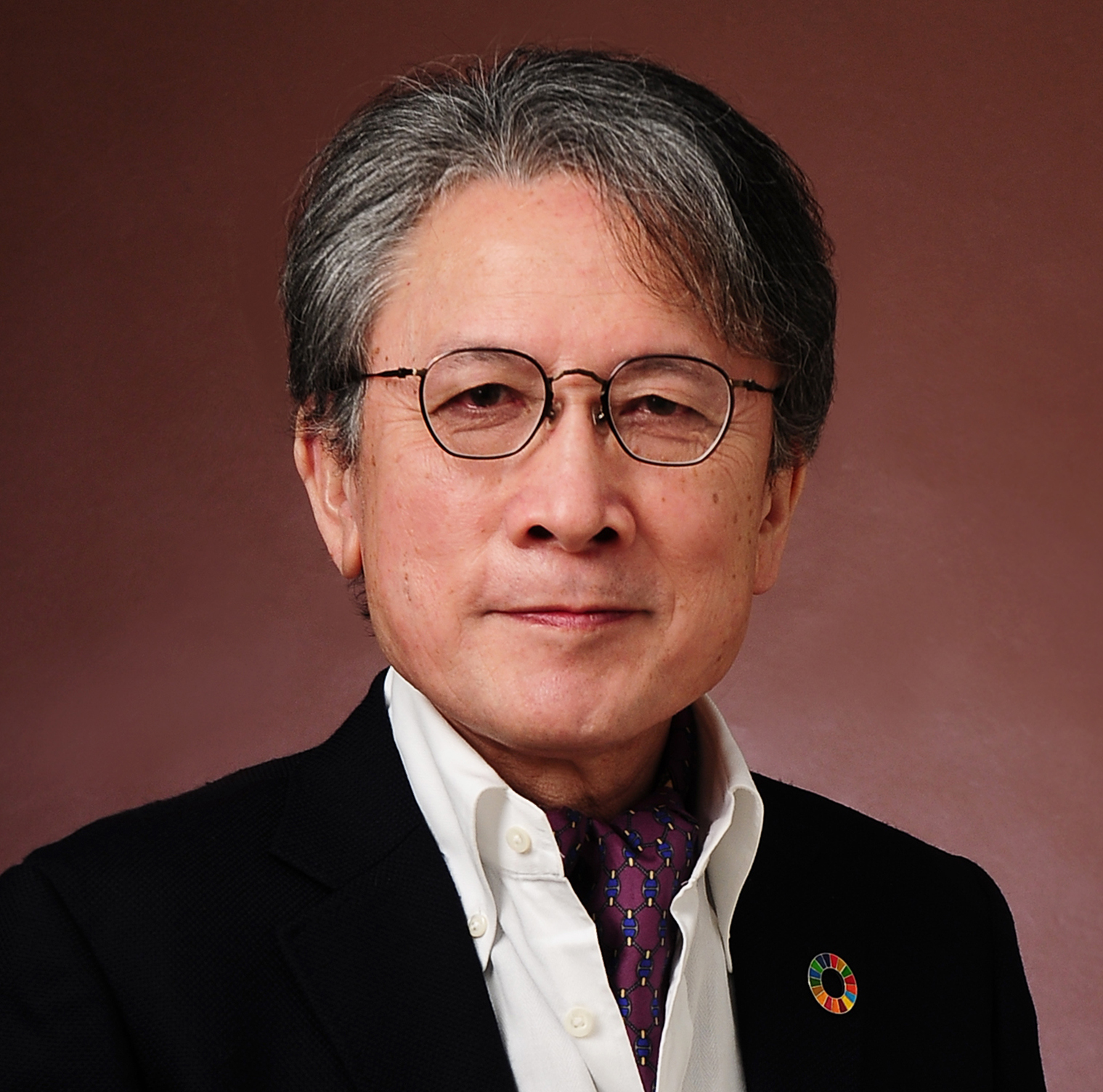
菊田 一郎(きくた・いちろう)
エルテックラボ 代表/物流ジャーナリスト
1982年名古屋大学経済学部卒業。物流専門出版社に37年間勤務し月刊誌編集長、代表取締役社長、関連団体役員等を兼務歴任。この間、国内・欧米・アジアの物流現場・企業取材を約1,000件実施、講演・寄稿など外部発信も多数。 2020年6月に独立し現職。物流、サプライチェーン・ロジスティクス分野のデジタル化・自動化/DX、SDGs/ESG対応等のテーマにフォーカスし、著述、取材、講演、アドバイザリー業務等を展開中。17年6月より㈱大田花き 社外取締役、20年6月より23年6月まで㈱日本海事新聞社顧問、20年後期より流通経済大学非常勤講師、21年1月よりハコベル㈱顧問。 著書に「先進事例に学ぶ ロジスティクスが会社を変える」(白桃書房、共著)、ビジネス・キャリア検定試験標準テキスト「ロジスティクス・オペレーション3級」(中央職業能力開発協会、11年・17年改訂版、共著)、「物流センターシステム事例集1~7」(流通研究社、単著)など。
お客様の考えるレベルにあわせて
省力化・自動化をかなえるYEデジタルの物流ソリューション
『MMLogiStation』
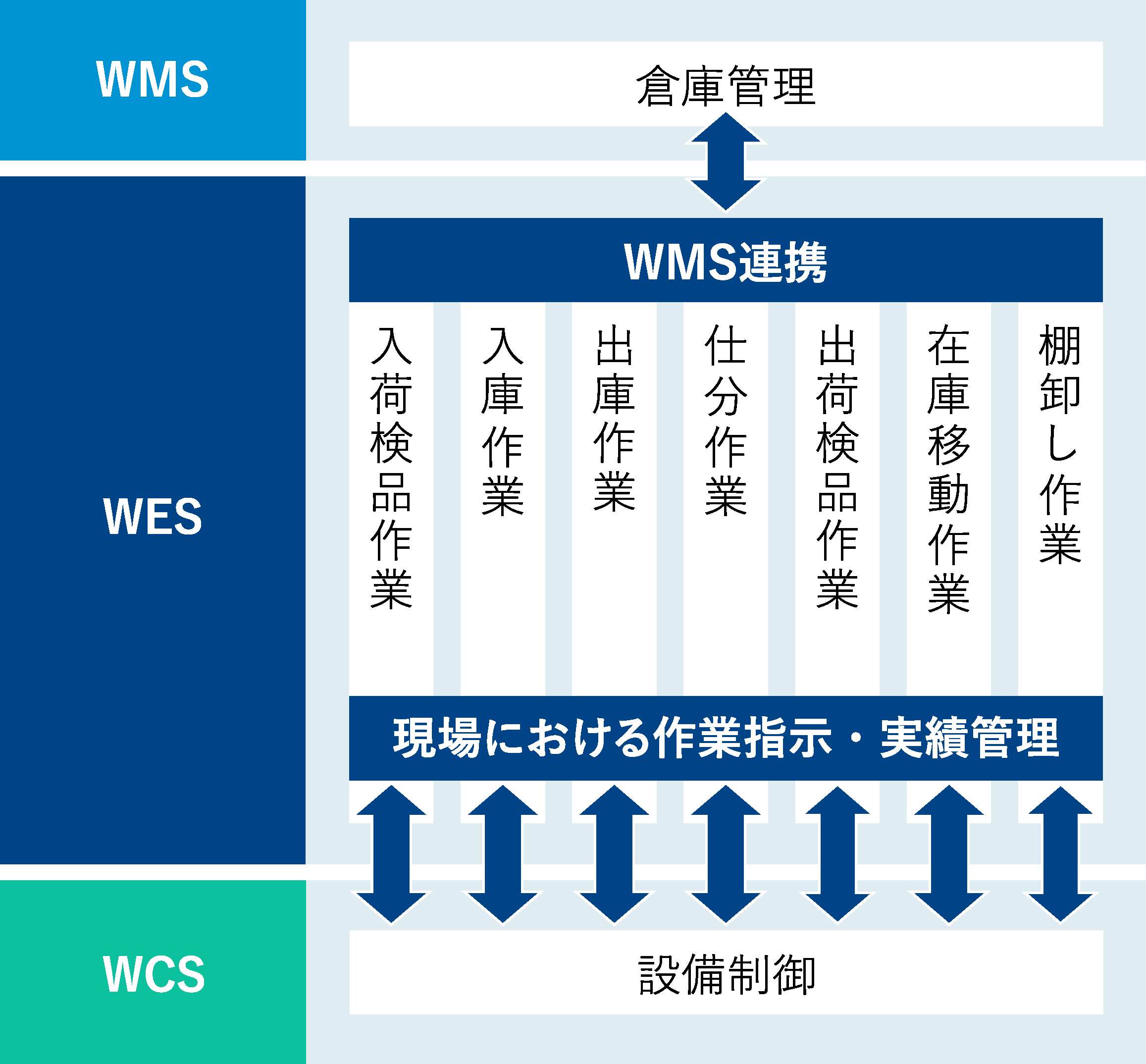
WES(倉庫実行システム)とは?
物流倉庫業務における基幹システムで、原料や在庫といった物の管理を行うWMS(倉庫管理システム)と、倉庫内の設備のリアルタイム制御を行うWCS(倉庫制御システム)の間で、「物流現場の制御・管理に特化」したシステムのこと。 従来WMSが行っていた現場の制御と管理をWESに分離することで、WMSの役割がシンプルになり、自動化設備の導入や作業手順の変更等、業務の変化にスピーディーに対応することが可能となります。